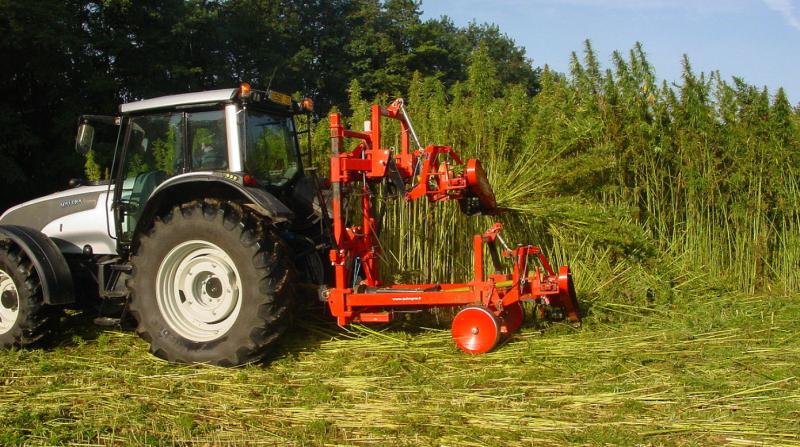
Vertical integration, the practice of controlling every stage of production, from raw materials to finished goods, is a seductive proposition for hemp businesses. By owning the entire supply chain, companies aim for increased efficiency, cost savings, and higher profit margins. However, the reality of vertical integration in the hemp industry often presents a formidable financial hurdle.
The Cost Breakdown:
- Farm-to-Table (Food):
- Cultivation:
- Land Acquisition/Lease: Significant upfront investment, especially for prime agricultural land.
- Infrastructure: Building greenhouses, irrigation systems, and storage facilities.
- Labor: Hiring skilled agricultural workers for planting, harvesting, and pest control.
- Equipment: Tractors, harvesters, and specialized equipment for hemp cultivation.
- Seed Sourcing: Ensuring high-quality, consistent seed supply.
- Processing:
- Extraction: Investing in sophisticated extraction equipment (e.g., CO2 extraction) and skilled operators.
- Refining: Refining hemp oil into food-grade products like hemp seed oil, protein powder, and hemp hearts.
- Packaging & Distribution: Investing in packaging lines, transportation, and a robust distribution network.
- Research & Development: Continuous investment in research to improve cultivation techniques, extraction methods, and product development.
- Cultivation:
- Farm-to-Floor (Industrial Hemp):
- Cultivation: Similar costs to food production, with a focus on fiber and grain varieties.
- Processing:
- Fiber Processing: Investment in decortication, scutching, and spinning machinery to convert hemp stalks into fibers.
- Grain Processing: Investing in equipment for cleaning, milling, and processing hemp seeds for animal feed and other uses.
- Wood Processing: If utilizing hempwood, investing in sawmills, kilns, and wood processing equipment.
- Manufacturing:
- Textile Production: Investing in looms, knitting machines, and dyeing equipment for fabric production.
- Construction Materials: Investing in equipment for producing hempcrete, hemp-based composites, and other building materials.
Beyond Capital Expenditures:
- Regulatory Compliance: Navigating a complex regulatory landscape with varying state and federal laws adds significant costs.
- Quality Control: Maintaining consistent quality throughout the entire supply chain requires rigorous testing and quality control measures.
- Inventory Management: Managing inventory across multiple stages of production can be challenging and costly.
- Risk Mitigation: Insuring against crop failures, market fluctuations, and other potential risks is crucial.
The Potential Rewards:
Despite the significant costs, vertical integration offers potential rewards:
- Improved Profit Margins: Eliminating intermediaries can increase profitability.
- Enhanced Quality Control: Greater control over the entire process allows for stricter quality standards.
- Brand Differentiation: Offering unique, vertically integrated products can create a strong brand identity.
- Increased Market Share: Controlling the supply chain can provide a competitive advantage.
Conclusion:
Vertical integration in the hemp industry presents both significant challenges and potential rewards. Careful planning, robust financial modeling, and a deep understanding of the market are essential for success. While the initial investment may be substantial, the long-term benefits of controlling the entire supply chain can be significant for businesses that can navigate the complexities and capitalize on the growing demand for hemp products.
Disclaimer: This article provides general information and should not be considered financial advice.
Note: This article provides a general overview. The actual costs of vertical integration will vary significantly depending on the specific products, scale of operations, and chosen business model.
Sources: